پرنٹنگ ٹیکنالوجی کی مسلسل ترقی کے ساتھ، بہت سے معروف پرنٹنگ برانڈز کے آلات کی کارکردگی نہ صرف بہتر سے بہتر ہوئی ہے، بلکہ آٹومیشن کی ڈگری میں بھی مسلسل بہتری آئی ہے۔ سیاہی کا رنگ ریموٹ کنٹرول سسٹم بہت سی ذہین پرنٹنگ کی "معیاری ترتیب" بن گیا ہے، جس سے پرنٹ شدہ مصنوعات کے سیاہی رنگ کے کنٹرول کو آسان اور قابل اعتماد بنایا گیا ہے۔ تاہم، اصل پرنٹنگ کے عمل میں، پرنٹ شدہ مصنوعات کے ہر بیچ کے لیے مستحکم سیاہی کا رنگ حاصل کرنا آسان نہیں ہے۔ سیاہی کے رنگ میں بڑے فرق کی وجہ سے معیار کے مسائل اکثر پیداوار میں پیش آتے ہیں، جس سے کمپنی کو نقصان ہوتا ہے۔
پرنٹ کرنے سے پہلے، تجربہ کی بنیاد پر پری ایڈجسٹمنٹ کا اچھا کام کرنا ضروری ہے۔
سب سے پہلے، ثبوت کے علاقے کے مطابق ہر رنگ گروپ کے سیاہی فاؤنٹین کی سیاہی کا حجم تقریباً ایڈجسٹ کریں یاپرنٹنگپلیٹ یہ کام انک ریموٹ کنٹرول سسٹم سے لیس مشین پر مکمل کرنا آسان ہے۔ اس کے لیے 80% سے زیادہ کا تخمینہ ہونا چاہیے۔ رنگ کے بڑے فرق سے بچنے کے لیے پرنٹنگ کے دوران سیاہی کے حجم کو بڑی حد میں ایڈجسٹ نہ کریں۔
دوم، پروڈکشن پروسیس شیٹ کی ضروریات اور پروڈکٹ کی خصوصیات کے مطابق، رسمی پرنٹنگ کے دوران جلدی میں ہونے سے بچنے کے لیے فیڈر، کاغذ جمع کرنے، سیاہی کی کارکردگی، پریشر سائز اور دیگر لنکس کو پہلے سے ایڈجسٹ کریں۔ ان میں، اس بات کو یقینی بنانا کہ فیڈر کاغذ کو قابل اعتماد، مسلسل اور مستحکم طریقے سے کھا سکتا ہے۔ تجربہ کار آپریٹرز پہلے اڑانے، سکشن، پریشر فٹ، پریشر سپرنگ، پیپر پریسنگ وہیل، سائیڈ گیج، فرنٹ گیج وغیرہ کو کاغذ کی شکل اور موٹائی کے مطابق پہلے سے ایڈجسٹ کرتے ہیں، مختلف اجزاء کے درمیان موومنٹ کوآرڈینیشن رشتہ کو سیدھا کرتے ہیں، اس بات کو یقینی بنائیں کہ فیڈر کاغذ کو آسانی سے فیڈ کرتا ہے، اور فیڈر ٹکرانے کی وجہ سے سیاہی کے مختلف رنگوں سے بچیں۔ یہ سفارش کی جاتی ہے کہ تجربہ کار کارکن فیڈر کو پہلے سے ایڈجسٹ کر سکتے ہیں۔
اس کے علاوہ، سیاہی کی چپکنے والی، روانی اور خشکی کو استعمال شدہ کاغذ کے معیار اور پرنٹ شدہ پروڈکٹ کی تصویر اور ٹیکسٹ ایریا کے سائز کے مطابق اس کی پرنٹنگ کو بہتر بنانے اور عام پرنٹنگ کو یقینی بنانے کے لیے پہلے سے مناسب طریقے سے ایڈجسٹ کیا جانا چاہیے۔ . ربڑ کے کپڑے اور پرنٹنگ پلیٹ پر کاغذ کے بالوں اور سیاہی کی جلد کو صاف کرنے کے لیے بار بار بند ہونے کی وجہ سے سیاہی کا رنگ ناہموار نہیں ہونا چاہیے۔ اگر پرنٹنگ کے بیچ میں مختلف چپکنے والے ہٹانے والے اور سیاہی کے تیل کو شامل کیا جائے تو رنگ کا انحراف یقینی ہے۔
مختصراً، مشین کو شروع کرنے سے پہلے پہلے سے ایڈجسٹمنٹ کا اچھا کام کرنے سے رسمی پرنٹنگ کے بعد ناکامی کو بہت کم کیا جا سکتا ہے، اور کپتان کے پاس سیاہی کے رنگ پر توجہ دینے کے لیے وقت اور توانائی ہوگی۔
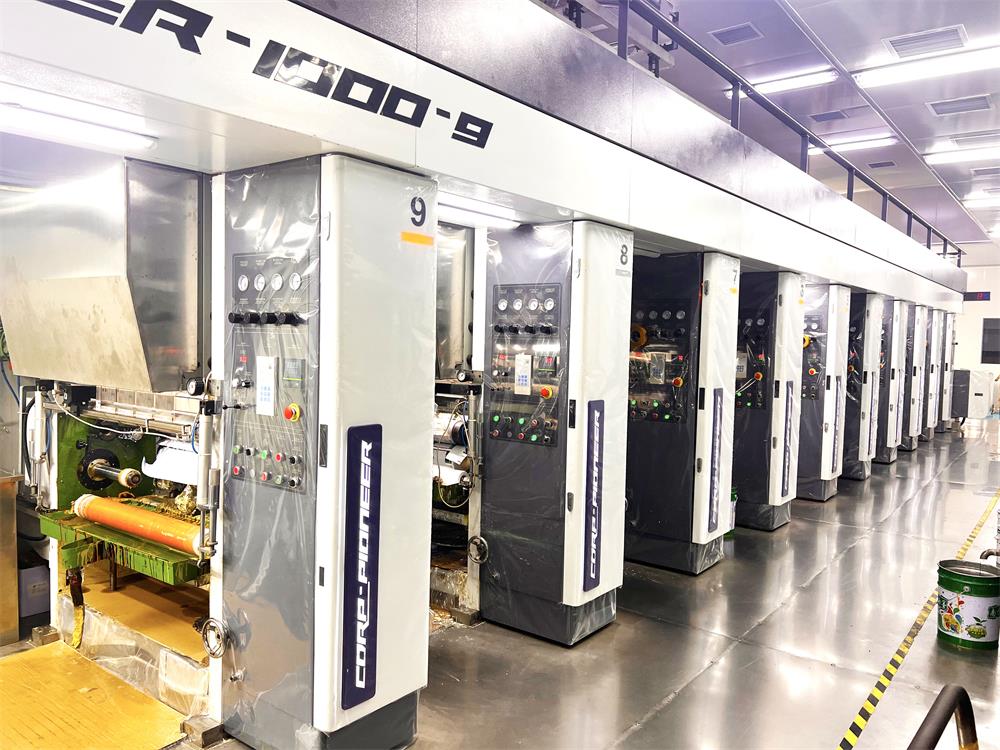
پانی اور انک رولر پریشر کو درست طریقے سے ایڈجسٹ کریں۔
پرنٹنگ کے عمل کے دوران، پرنٹنگ پلیٹ کی تصویر اور متن کے حصے کو مستقل اور یکساں طور پر سیاہی کی مناسب مقدار کے ساتھ لگانا چاہیے تاکہ مستقل سیاہی کے رنگ کے ساتھ پرنٹ حاصل کیا جا سکے۔ لہذا، سیاہی کے رولرس اور انک رولرس کے ساتھ ساتھ انک رولرس اور پرنٹنگ پلیٹ کو اچھی سیاہی کی منتقلی حاصل کرنے کے لیے مناسب رابطہ اور رولنگ تعلقات کو برقرار رکھنا چاہیے۔ اگر یہ کام احتیاط اور صحیح طریقے سے نہ کیا جائے تو سیاہی کا رنگ برابر نہیں رہے گا۔ لہذا، جب بھی پانی اور سیاہی کے رولرس نصب کیے جاتے ہیں، انک بار کو رول کرنے کا طریقہ تناؤ کو جانچنے کے لیے فیلر گیج کے استعمال کے روایتی طریقے کے بجائے، ان کے درمیان دباؤ کو ایک ایک کرکے ایڈجسٹ کرنے کے لیے استعمال کیا جاتا ہے، کیونکہ بعد میں مختلف انسانی عوامل کی وجہ سے ایک بڑی اصل غلطی، اور اس پر کثیر رنگ اور تیز رفتار مشینوں پر پابندی لگائی جانی چاہیے۔ جہاں تک رولنگ انک بار کی چوڑائی کا تعلق ہے، یہ عام طور پر 4 سے 5 ملی میٹر ہونا مناسب ہے۔ پہلے انک ٹرانسفر رولر اور انک سٹرنگنگ رولر کے درمیان پریشر کو ایڈجسٹ کریں، پھر انک رولر اور انک سٹرنگنگ رولر اور پرنٹنگ پلیٹ سلنڈر کے درمیان پریشر کو ایڈجسٹ کریں، اور آخر میں واٹر ٹرانسفر رولر، پلیٹ واٹر رولر، کے درمیان پریشر کو ایڈجسٹ کریں۔ واٹر سٹرنگ رولر اور انٹرمیڈیٹ رولر کے ساتھ ساتھ پلیٹ واٹر رولر اور پرنٹنگ پلیٹ سلنڈر کے درمیان دباؤ۔ ان آبی گزرگاہوں کے درمیان سیاہی کی بار 6 ملی میٹر ہونی چاہیے۔
آلات کو دو یا تین ماہ کے استعمال کے بعد دوبارہ ایڈجسٹ کرنے کی ضرورت ہے، کیونکہ انک رولر کا قطر تیز رفتار رگڑ کی مدت کے بعد چھوٹا ہو جائے گا، خاص طور پر ٹرانسمیشن میں۔ سیاہی رولرس کے درمیان دباؤ چھوٹا ہو جاتا ہے، اور جب سیاہی رولرس ان پر جمع ہو جائیں گے تو سیاہی منتقل نہیں ہو سکے گی۔ جب فیڈر پرنٹنگ جاری رکھنے کے لیے روکتا ہے یا رک جاتا ہے، اس وقت سیاہی بڑی ہوتی ہے، جس کی وجہ سے پہلی درجنوں یا یہاں تک کہ سینکڑوں شیٹس کی سیاہی کا رنگ گہرا ہو جاتا ہے، اور پانی کی سیاہی کا مثالی توازن حاصل کرنا مشکل ہوتا ہے۔ یہ خرابی عام طور پر تلاش کرنا آسان نہیں ہے، اور یہ صرف اس وقت زیادہ واضح ہوتا ہے جب باریک پرنٹس پرنٹ کرتے ہیں۔ مختصراً، اس سلسلے میں آپریشن پیچیدہ ہونا چاہیے اور طریقہ کار سائنسی ہونا چاہیے، ورنہ یہ پانی، سیاہی کی پٹی، منہ اور دم پر سیاہی کی مختلف گہرائیوں کا باعث بنے گا، جو مصنوعی طور پر خرابی کا باعث بنے گا اور مشکلات میں اضافہ ہو گا۔ آپریشن
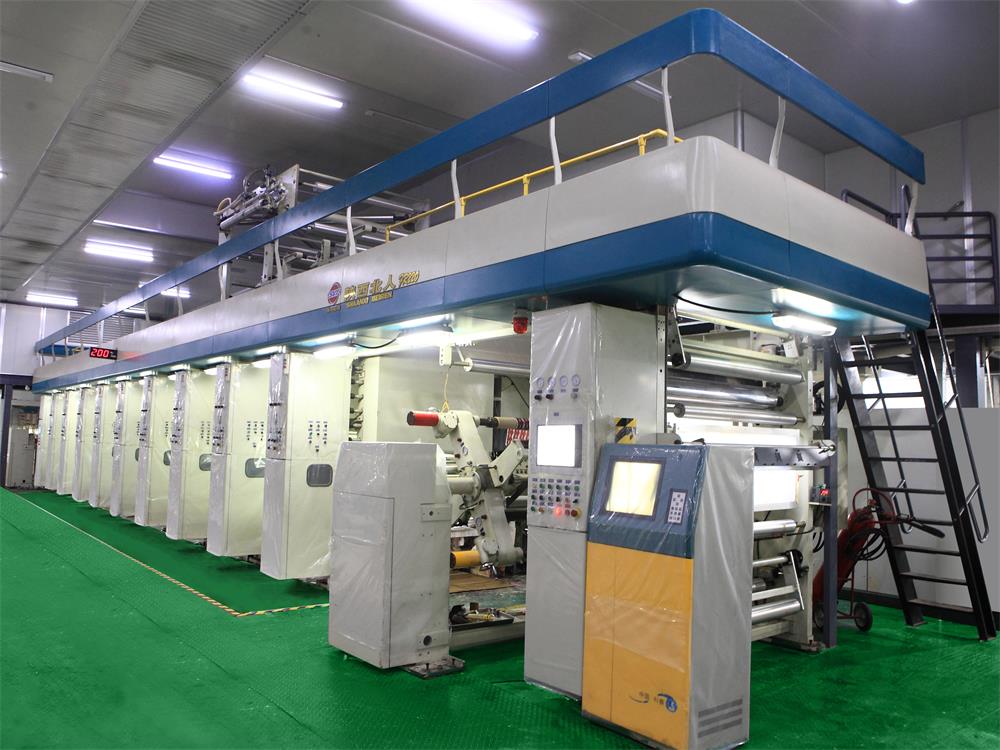
پانی کی سیاہی کا توازن حاصل کرنا
جیسا کہ ہم سب جانتے ہیں، پانی کی سیاہی کا توازن آفسیٹ پرنٹنگ کا ایک اہم حصہ ہے۔ اگر پانی بڑا ہے اور سیاہی بڑی ہے، تو سیاہی کو پانی میں تیل میں ملایا جائے گا، اور پرنٹ شدہ مصنوعات کا معیار یقینی طور پر مثالی نہیں ہوگا۔ طویل مدتی مشق کے ذریعے، مصنف نے کچھ تکنیکوں کی کھوج کی ہے۔
سب سے پہلے، اس بات کو یقینی بنائیں کہ پانی اور سیاہی کے رولرس کے درمیان دباؤ کا تعلق مناسب طریقے سے ایڈجسٹ کیا گیا ہے، اور فاؤنٹین سلوشن اور آئسوپروپل الکحل کا مواد عام معیارات پر پورا اترتا ہے۔ اس بنیاد پر، مشین کو آن کریں، پانی اور سیاہی کے رولرس کو بند کریں، اور پھر پرنٹنگ پلیٹ کو چیک کرنے کے لیے مشین کو روک دیں۔ پرنٹنگ پلیٹ کے کنارے پر ہلکی سی 3 ملی میٹر چپچپا گندگی رکھنا بہتر ہے۔ اس وقت پانی کی مقدار کو پرنٹنگ کے لیے ابتدائی پانی کی رقم کے طور پر لے کر، عام گرافک مصنوعات کی عام پرنٹنگ کی ضمانت دی جا سکتی ہے، اور پانی کی سیاہی کا توازن بنیادی طور پر حاصل کیا جا سکتا ہے۔
دوم، پانی کی مقدار کو دیگر عوامل کے مطابق لچکدار طریقے سے ایڈجسٹ کیا جا سکتا ہے، جیسے پرنٹنگ پلیٹ کا بڑا رقبہ، کاغذ کی کھردری سطح، سیاہی میں اضافے کی ضرورت، پرنٹنگ کی رفتار اور اس میں تبدیلیاں۔ ہوا کا درجہ حرارت اور نمی۔
اس کے علاوہ، مصنف نے یہ بھی پایا کہ جب مشین ابھی پرنٹ کرنا شروع کی جاتی ہے، جسم کا درجہ حرارت کم ہوتا ہے، اور جب مشین ایک یا دو گھنٹے تک تیز رفتاری سے چلتی ہے، تو جسم کا درجہ حرارت، خاص طور پر ربڑ رولر کا درجہ حرارت بڑھ جاتا ہے۔ دوگنا سے زیادہ، یا اس سے بھی زیادہ اضافہ۔ اس وقت، پانی کی مقدار کو آہستہ آہستہ بڑھایا جانا چاہئے جب تک کہ پانی کی سیاہی ایک نئے توازن تک نہ پہنچ جائے۔
یہ دیکھا جا سکتا ہے کہ پانی کی سیاہی کا توازن حاصل کرنا آسان نہیں ہے، اور آپریٹر کو اسے وزن اور جدلیاتی طور پر استعمال کرنے کی ضرورت ہے۔ دوسری صورت میں، سیاہی کے رنگ کے استحکام کو کنٹرول کرنا مشکل ہے، اور اعلی معیار کی پرنٹ شدہ مصنوعات کو پرنٹ نہیں کیا جا سکتا.
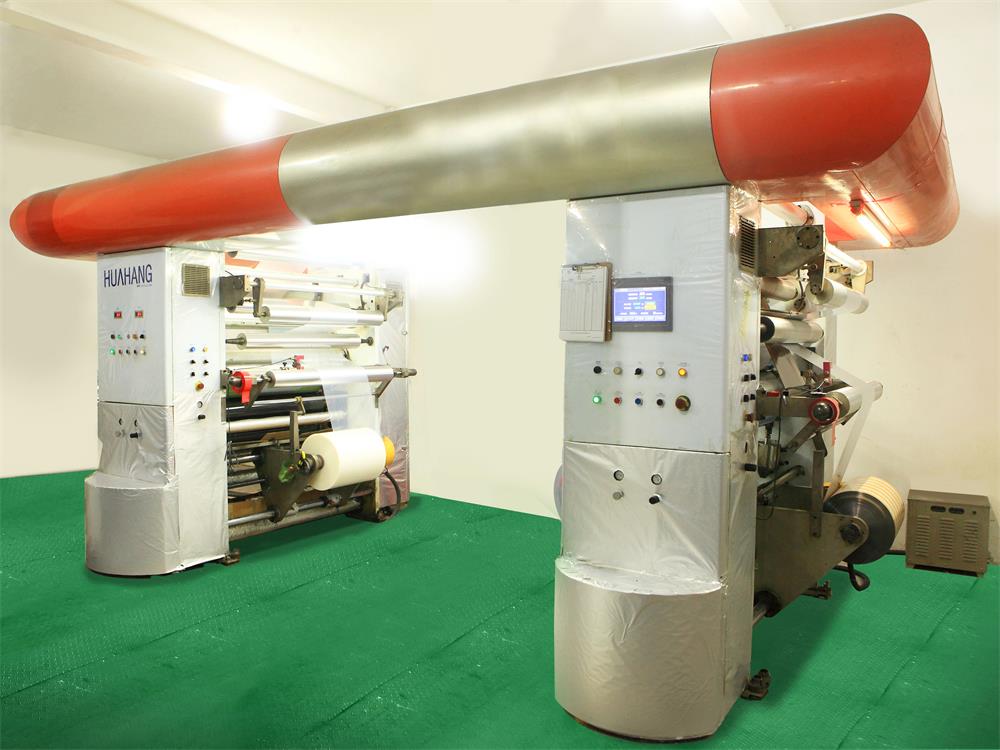
پروف ریڈنگ اور رنگ کی ترتیب کا انتظام
پیداوار میں، ہمیں اکثر ایسی صورت حال کا سامنا کرنا پڑتا ہے: گاہک کی طرف سے فراہم کردہ نمونہ انتہائی غیر معیاری ہے، یا بغیر ثبوت کے صرف رنگین انک جیٹ ڈرافٹ فراہم کیا جاتا ہے۔ اس وقت، ہمیں مخصوص صورتحال کا تجزیہ کرنے کی ضرورت ہے، اور ہم ثبوت کے اثر کا پیچھا کرنے کے لیے سیاہی کے حجم کو سختی سے بڑھانے یا کم کرنے کا طریقہ استعمال نہیں کر سکتے۔ یہاں تک کہ اگر یہ شروع میں ثبوت کے قریب ہے، سیاہی کے رنگ کے استحکام کی ضمانت نہیں دی جاسکتی ہے، اور اس طرح پرنٹ شدہ مصنوعات کے حتمی معیار کی ضمانت نہیں دی جاسکتی ہے. اس سلسلے میں، پرنٹنگ فیکٹری کو گاہک کے ساتھ سنجیدہ اور ذمہ دارانہ رویہ کے ساتھ فعال طور پر بات چیت کرنی چاہیے، نمونے کے مسائل اور ترمیم کی تجاویز کی نشاندہی کرنا چاہیے، اور رضامندی حاصل کرنے کے بعد پرنٹ کرنے سے پہلے مناسب ایڈجسٹمنٹ کرنا چاہیے۔
پیداوار میں، ایک کثیر رنگ کی مشین کی پرنٹنگ رنگ ترتیب عام طور پر سیاہی کی viscosity کی طرف سے مقرر کیا جاتا ہے. چونکہ ملٹی کلر پرنٹنگ میں، سیاہی کو گیلے گیلے انداز میں سپر امپوز کیا جاتا ہے، صرف بہترین سپر امپوزیشن ریٹ حاصل کرنے سے ہی ایک مستحکم اور مستقل سیاہی کا رنگ پرنٹ کیا جا سکتا ہے۔ پرنٹنگ رنگ کی ترتیب کو پرنٹ شدہ مصنوعات کی خصوصیات اور معیار کے تقاضوں کے مطابق ہونا چاہیے، اور کوئی تبدیلی نہیں رہ سکتی۔ ایک ہی وقت میں، سیاہی کی viscosity کو بھی ایڈجسٹ کیا جا سکتا ہے. مثال کے طور پر، جامنی رنگ کے کور اور اسکائی بلیو کور میں پرنٹنگ رنگ کے مختلف سلسلے ہوتے ہیں: پہلے کے لیے سیان پہلے اور میجنٹا سیکنڈ اور میجنٹا پہلے اور بعد کے لیے سیان سیکنڈ۔ بصورت دیگر، اوور پرنٹ شدہ رنگ نظر آئیں گے، جو نہ تو ہموار ہیں اور نہ ہی مستحکم۔ مثال کے طور پر، ایک پرنٹ کے لیے جو بنیادی طور پر سیاہ ہے، سیاہ کو آخری رنگ کے گروپ میں جتنا ہو سکے رکھا جانا چاہیے۔ اس طرح، سیاہ کی چمک بہتر ہوتی ہے اور مشین کے اندر خروںچ اور رنگ کے اختلاط سے بچا جاتا ہے۔
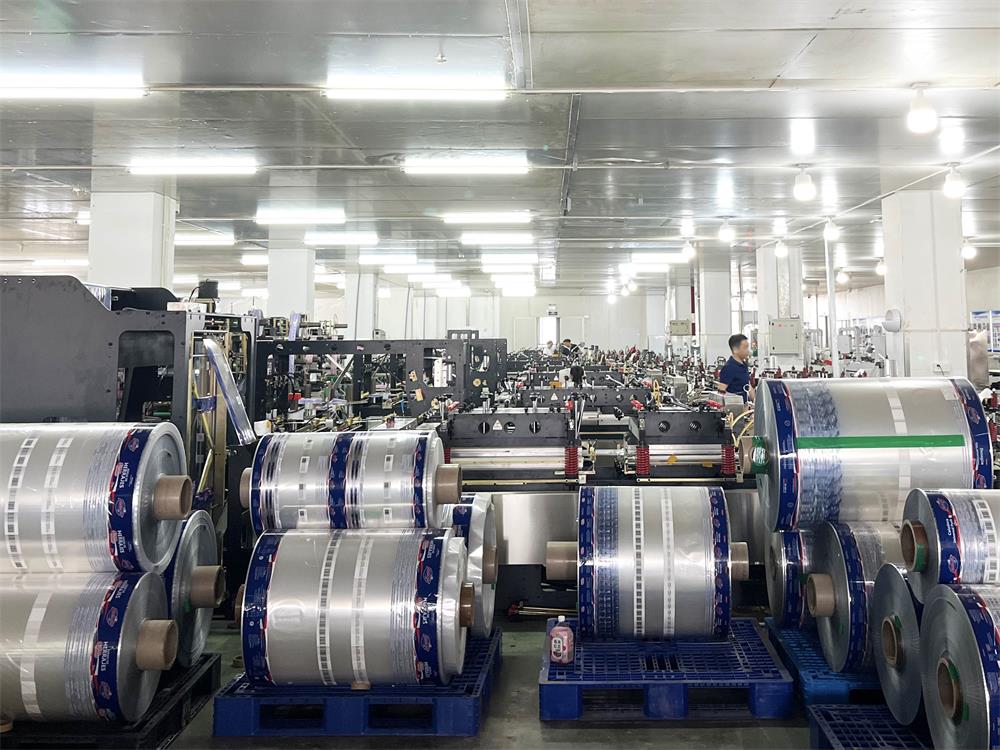
اچھی آپریٹنگ عادتیں پیدا کریں اور کام کی ذمہ داری کو مضبوط کریں۔
کوئی بھی کام کرتے وقت ہمیں ذمہ داری کا اعلیٰ احساس اور معیار کا مضبوط احساس ہونا چاہیے۔ ہمیں عمل کو معیاری بنانا چاہیے اور اچھی روایتی عادات جیسے "تین درجے" اور "تین محنت" کی پابندی کرنی چاہیے۔ نمونوں کے متواتر موازنہ کو بطور مثال لیں۔ نمونے پر دستخط کے نمونے کا موازنہ کرتے وقت، فاصلے، زاویہ، روشنی کے منبع، وغیرہ میں فرق کی وجہ سے، بصری متعصب ہوگا، جس کے نتیجے میں سیاہی کا رنگ متضاد ہوگا۔ اس وقت، دستخط کے نمونے کو نمونے سے اتار کر احتیاط سے موازنہ کرنا چاہیے۔ طویل عرصے سے چلنے والی پرنٹنگ پلیٹ کو بیک کرنے کی ضرورت ہے تاکہ پلیٹ کی تبدیلی کی وجہ سے سیاہی کے رنگ کے انحراف کو کم کیا جا سکے۔ ربڑ کے کپڑے کو کثرت سے صاف کیا جانا چاہیے، اور سیاہی کا رنگ مستحکم کرنے کے لیے ہر صفائی کے بعد مزید بلوٹنگ پیپر رکھنا چاہیے۔ فیڈر کے موقوف ہونے کے بعد، پانچ یا چھ شیٹس جو ابھی پرنٹ کی گئی ہیں بہت سیاہ ہیں اور انہیں نکالنے کی ضرورت ہے۔ پرنٹنگ کی رفتار زیادہ تیز نہیں ہونی چاہیے۔ اہم بات مشین کو مستحکم اور نارمل رکھنا ہے۔ سیاہی کے چشمے میں سیاہی ڈالتے وقت، کیونکہ نئی سیاہی سخت ہے اور اس کی روانی کم ہے، اس لیے اسے کئی بار ہلانا چاہیے تاکہ سیاہی کی مقدار متاثر نہ ہو اور سیاہی کے رنگ میں انحراف نہ ہو۔
آپریٹرز کو سیکھنا، مشاہدہ کرنا اور تجزیہ کرنا جاری رکھنا چاہیے، تمام پہلوؤں سے سیاہی کے رنگ کی تبدیلی کو متاثر کرنے والے عوامل کا پتہ لگانا چاہیے، اور ان کو صحیح طریقے سے روکنے اور اس پر قابو پانے کے لیے متعلقہ اقدامات کرنا چاہیے، سیاہی کے رنگ کے استحکام اور مستقل مزاجی کو بہتر بنانے کی کوشش کرنی چاہیے۔ طباعت شدہ مصنوعات، اور مؤثر طریقے سے طباعت شدہ مصنوعات کے معیار کو بہتر بنائیں۔
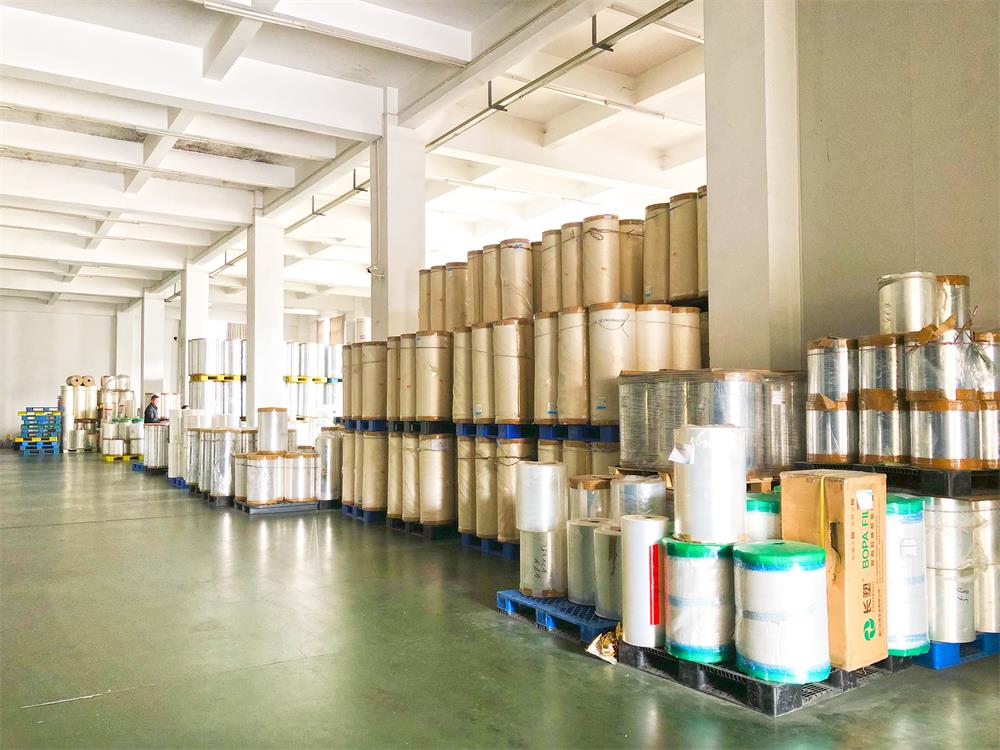
پوسٹ ٹائم: مئی 27-2024